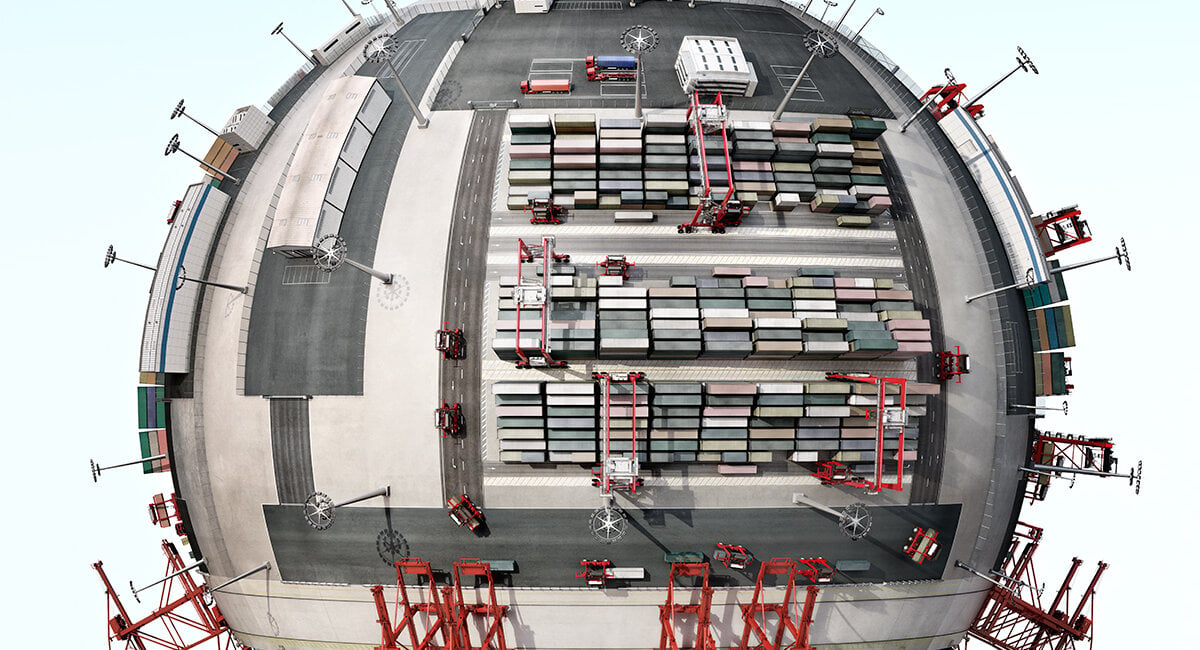
OneTerminal enables a smooth, flexible path to RTG automation for brownfield terminals
Automating an existing rubber-tyred gantry crane (RTG) terminal requires extensive expertise, thorough planning, comprehensive training and careful change management. The OneTerminal AutoRTG concept is a pre-tested and integrated solution being developed by Kalmar and Navis to address the unique requirements of brownfield terminals. It is designed to make the whole process as smooth as possible, providing the flexibility to adopt automation at a pace that suits the needs of each individual terminal.
RTGs are the most popular equipment choice for container stacking at terminals around the world, especially where high-capacity stacking and good manoeuvrability are key requirements. Today, approximately 60% of the world’s container terminals use RTGs for container stacking operations.
Manual RTG operations present a variety of different challenges for terminal operators, with inflexibility and less-than-ideal working conditions being the most significant. Not only does each individual crane require a dedicated operator, but valuable time is lost when transferring operators between cranes. On top of all that, working conditions inside an RTG cabin can become uncomfortable, with operators working long shifts – sometimes in extremely hot or cold conditions – and having to climb out of the cabin and walk some distance to access bathroom facilities.
Why automate RTG operations?
Automating your RTG operations brings a variety of benefits, the immediate and easily quantified being significant savings in operating expenses. Furthermore, with fewer people working in the yard area, occupational safety is significantly improved because there is a much lower risk of accidents. Other benefits include increased efficiency, more predictable operations, higher availability, better site security and longer equipment life spans.
With some level of automation in place, a terminal can react faster to changing operational needs. Not only can operators swap from machine to machine in seconds rather than tens of minutes, but they can also oversee multiple cranes at a time. Furthermore, as the job moves from cabin to control room the working environment becomes clean, safe and comfortable – making recruitment easier too.
Automating RTG operations brings significant savings in operating expenses.
Smoothing the way with a pre-integrated, single-vendor solution
OneTerminal is a standardised automation solution delivered by one team, with one process and one ambition. If automation is built with a non-holistic and fragmented approach, the terminal may be able to cut costs in the short term, but these savings can be wiped out at the deployment stage due to the added complexity of integration and slower ramp-up of productivity.
OneTerminal eliminates this problem by delivering the Navis N4 TOS (Terminal Operating System) and the Kalmar TLS (Terminal Logistics System) equipment control system as a pre-integrated and tested solution. Combining these systems into one package helps to alleviate the implementation challenges that many terminals can face with the multi-vendor approach.
Kalmar performs release tests for every major new version of Navis N4 with the latest version of the Kalmar TLS. While the pre-integration work does not cover customer-specific process flows and configuration, it does significantly reduce the risk and workload associated with these activities.
Furthermore, OneTerminal projects are delivered by one team of experts from Navis and Kalmar, who take full accountability for the automation project. With OneTerminal, terminal operators will have project control with a clear governance structure for faster decision-making and execution.
Phased implementation at a comfortable pace
In today’s fast-paced industry where terminal operators are driven by the need to maintain efficiency and profitability, slowing down or completely halting operations to implement automation simply isn’t an option.
In existing terminals, operators need to carefully plan and build an automation roadmap that suits their unique set of circumstances and then roll out the solution at their own pace. This type of phased implementation eliminates the risk of disruption to operations and revenue streams, with the opportunity to implement automation one container block at a time. This allows operators to familiarise themselves with the hardware and software using selected equipment. Importantly, this is not a one-way street: switching individual cranes from manual to automated operation and back again is relatively straightforward, and does not impact the operation of the manual cranes in the fleet.
When considering automation, the customer can opt for a standardised automation package with OneTerminal, which minimises risks and allows faster and easier deployment to customer’s existing operations, or look at a customised solution based on individual customer requirements.
OneTerminal also provides the flexibility for terminals to increase the level of automation in line with business needs. A project typically begins with process automation alongside equipment automation – in this case for RTGs. Automation can then progress from remote control and remote control with driver assistance, where a single operator can control multiple RTGs, through to semi and fully automated RTG operations.
OneTerminal provides flexibility for terminals.
Practical considerations for operators considering RTG automation
Automation is as much, if not more, about a mindset change as a physical and technological shift. Automation represents a huge change for terminal personnel, requiring new skill sets, new tasks and an open dialogue between all teams involved.
A typical approach is to first initiate an implementation project to upgrade the TOS, which can be done independently of upgrading any existing Kalmar RTGs and third-party machines with the Kalmar TLS.
If there isn’t one already in place, a position detection system for road trucks will also need to be planned and implemented. Once proof of concept has been successfully achieved for the automated block, the terminal can roll the solution out to other blocks and gradually increase the level of intelligence and automation features.
Furthermore, although automated terminals provide significant improvements in occupational safety by keeping people out of areas where heavy machinery is operating, it is important to point out that any terminal looking to adopt automation for its RTGs must analyse and fulfil all the relevant safety requirements.
The future of RTG operations
OneTerminal combines the technologies and expertise of two of the industry’s leaders in equipment automation and terminal operating system solutions. The standardised, measured, and phased approach provides terminal operators with the flexibility to introduce automation at a pace that suits their business needs, without affecting existing terminal operations or risking profitability. What’s more, with pre-integration built in, terminal operators can save valuable time, money and hassle, and focus on implementing a solution that delivers the best possible business results. Most importantly, OneTerminal provides the fastest way to move to zero accidents on site.
The OneTerminal AutoRTG solution is currently under development and is expected to be available for proof-of-concept projects during the first quarter of 2019.
Hannu Karp, Product Manager, Kalmar, Antti Sutela, Product Manager, Kalmar, Floris Vernooij, Product Manager, Navis and Lucia Ramos, Product Portfolio Manager, Navis
Related articles
Subscribe and receive updates in your email
Subscribe