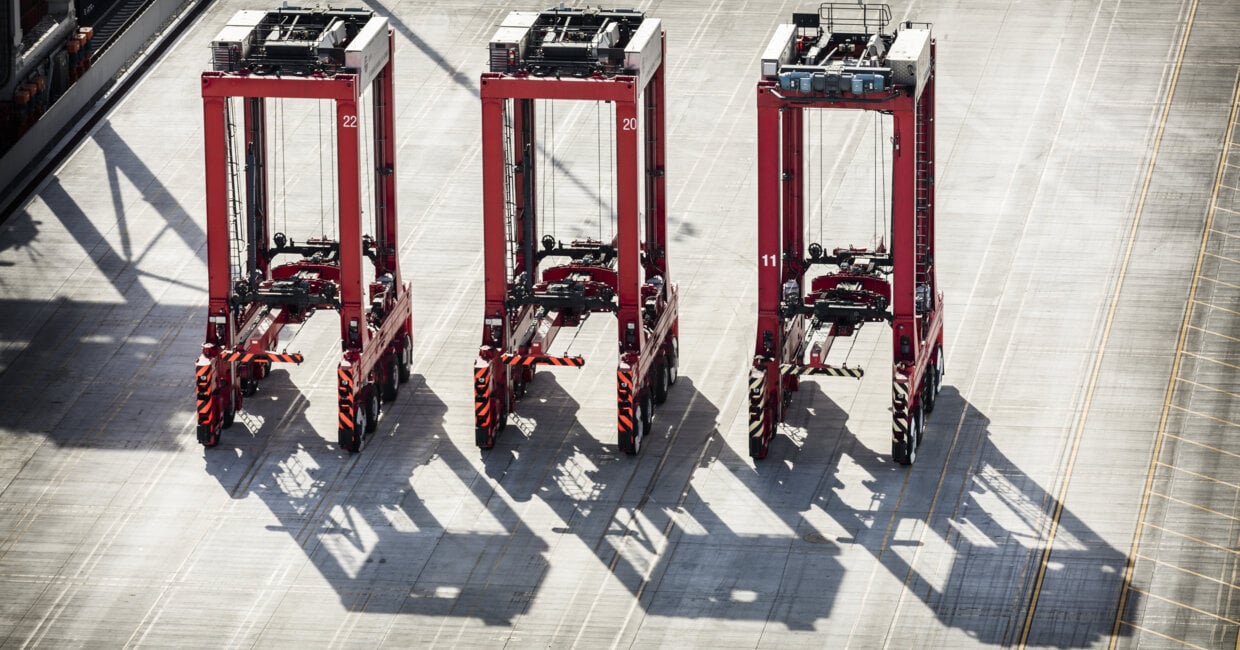
Streamline your straddle operations with Kalmar One
Kalmar’s versatile, scalable Automated Straddle Carrier application, powered by the Kalmar One automation system, offers a host of benefits for both greenfield and brownfield terminals in the marine and intermodal market segments. In this article, we take a closer look at how Kalmar’s intelligent, flexible technology makes terminal automation easy, efficient and cost-effective.
The flexible and scalable Kalmar One open automation system provides proven functionalities and well-established processes that enable terminals to streamline and automate their operations. Built-in standardisation makes it quicker, easier and more cost-effective for terminals to deploy, and it provides a rock-solid automation foundation that allows terminals to improve their efficiency, maintain the highest levels of safety and reduce their carbon emissions. Kalmar One is the automation brain behind the Kalmar Automated Straddle Carrier application, which features the Kalmar AutoStrad™ – our proven solution for automating quay, stack and landside operations with a single equipment type.
Safe, cost-competitive and flexible
Automated straddle carrier operations are ideal for medium-sized and large terminals where safety, high equipment flexibility and minimal labour costs are key requirements. “Automated straddle carriers operate within a fenced-off area, which physically segregates people from potential hazards, and of course there is no driver on board,” explains Jarkko Mäkiranta, Sales Director, Kalmar. “When people do need to access the operational area it can be done safely through designated, controlled access points. What’s more, with AutoStrad™ customers can move personnel away from the harsh environment of the yard and into a comfortable, ergonomic workstation with a remote control desk. From there they can take care of any exception handling.
With its low deployment and operating costs, the Kalmar automated straddle carrier application can help terminals to improve their cost competitiveness too. “Compared with a rail-mounted or stacking crane set up, for example, automated straddle carriers require lower investment in infrastructure because they can operate on regular asphalt with no special groundworks required,” Jarkko highlights. “At a basic level all that’s needed is the navigation hardware and software and the physical fencing around the operating area and you can get started.”
Automated straddle carriers are also proven to have a longer operational lifespan than equivalent manually operated machines. “In our experience, we see lifespans of around 15 years, which is about three to four years longer than a manual machine,” Jarkko says. “There’s also the added advantages of a short time to value, with the average project taking around two to three years to plan and implement, and the fact that the assets – the machines themselves – can easily be relocated between terminals as requirements change.”
In terms of operational flexibility, an automated straddle carrier setup enables a streamlined, simplified container flow, with only one type of equipment needed to process containers as soon as they leave the vessel and are grounded in the yard. “This is a clear advantage when it comes to optimising your terminal operations and also your maintenance planning and execution,” Jarkko points out. “This setup is a powerful, scalable tool for operations managers because it allows them to easily allocate resources and make sound operational decisions that optimise container flow for the situation in question.”
A big lift for marine and intermodal terminal operations
With the Kalmar Automated Straddle Carrier application, the typical setup is that the automated straddle carriers are used to serve a larger crane, for example, a quay crane in a marine terminal or a rail-mounted gantry crane (RMG) in an intermodal rail yard. There may also be a truck transfer area on the landside, where we can implement the Kalmar automated truck handling solution.
The Kalmar One automation system covers three layers: the terminal layer, the yard layer and the equipment layer. “To facilitate servicing, the yard layer can include a safe area for personnel and maintenance vehicles, enabling people and automated machines to coexist in a safe, controlled manner,” Jarkko says.
“We are the only vendor who can fully automate operational flows, whether from a quay crane to a truck or from an RMG to a truck, and we have many successful systems running at terminals around the world,” Jarkko highlights. “We can clearly demonstrate that our automation system extends the lifespan of the straddles themselves and is flexible and configurable to meet every operational need,” he continues. “Furthermore, we can support several different positioning solutions too.”
Smart safety and a flexible powertrain portfolio
Safety is always at the top of the priority list with any automated system, and Kalmar’s answer to this is the Smart Safety concept. “We can get rid of the need for physical fencing to segregate people and machinery by replacing it with geofencing, which enables flexible segregation and removes the need for residual hazard zones,” points out Jarkko. “Our application is easy to adapt to local operational use cases, meets all applicable safety standards in the US, Europe and Australia and is third-party approved by the classification society DNV.”
As with manually operated straddle carriers, the Kalmar AutoStrad™ itself is available in diesel-electric, hybrid and FastCharge™ configurations, so customers have the full range of powertrain alternatives to choose from depending on their operational needs. Stacking heights range from a unique 1 over 0 configuration up to 1 over 3, the machine is available with either a narrow or standard frame width and all typical load-handling modes are supported.
Proven success in all corners of the world
Kalmar AutoShuttles can be seen hard at work in Australia’s first fully automated container terminal, VICT in Melbourne, where they serve 20 Kalmar ASCs. At TraPac in Los Angeles, which is both a marine and an intermodal terminal, 40 Kalmar automated straddle carriers both feed the terminal’s 29 Kalmar ASCs and operate a stacking yard for containers. Patrick Terminals operates 27 Kalmar automated straddle carriers at its Brisbane AutoStrad™ Terminal and 44 at its Sydney AutoStrad™ Terminal. In Sydney, Kalmar is helping logistics services provider Qube build a fully automated intermodal terminal as part of the 243-hectare Moorebank Logistics Park (MLP) project. At MLP there will be eight Kalmar FastCharge automated straddle carriers serving intermodal yard cranes and trucks with fully automated truck handling and a warehouse interface.
One of the most recent ongoing projects is at Yara's Porsgrunn facility in Norway, where Kalmar is in the process of delivering fully autonomous equipment, software and services for a unique, fully digitalised container handling solution. This project will include three Kalmar FastCharge AutoStrad™ to replace traditional truck traffic.
“Our Kalmar AutoStrad™ application has a solid 15-year track record and we are delivering projects to some of the world’s biggest and most advanced new terminal developments, as well as to many brownfield sites. The success we have had is because of our ability to fully automate the cargo flows end to end by integrating our AutoStrad™, ASC and automated truck handling solutions,” Jarkko concludes.
Related articles
Further reading
Subscribe and receive updates in your email
Subscribe