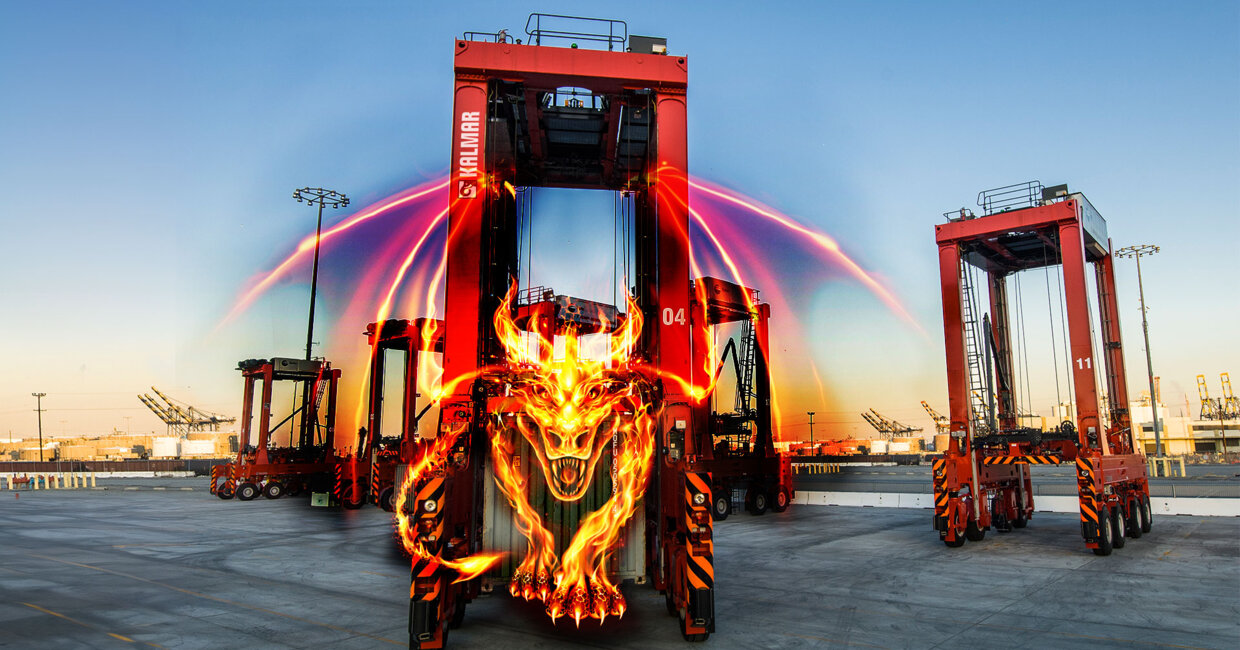
Myth #2: Automated straddle carriers can’t be used in megaterminals
There is a common misconception that automated straddle carriers are only suited for small and medium-sized container terminals. This erroneous belief perhaps stems from the early days of AutoStrad™ terminals when the technology was not yet proven over nearly two decades of continuous use around the world.
So, is it true that automated straddle carriers can't handle megaterminals (which we at Kalmar define as those with a capacity of more than 1M TEU/year)? In a word, no. Not only are automated straddle carriers suited for the same types of terminals as manual straddles, but they also enable a completely different level of flexibility than traditional gantry crane concepts. The Kalmar AutoStrad™ solution scales easily to fleets of up to hundreds of machines, making it suitable for even the largest terminals in the world.
Higher is not always better
For the largest container terminals, maximum stacking capacity and throughput are obviously key considerations. Traditionally, ASC and RTG cranes have been the default choice for these terminals, but the equation is no longer as clear-cut as it once was.
ASCs and RTGs do offer very high stacking capacity, but it will always be tied to the specific area under the crane. By contrast, automated straddle carriers can utilise space at the terminal more flexibly and deploy capacity whenever and wherever it is needed. The AutoStrad™ fleet can be shifted flexibly between the landside and waterside, whereas at an ASC terminal with a perpendicular layout, half of the container handling capacity is usually allocated to the waterside and half to the truck lanes.
It is worth noting that even though ASCs offer a theoretical stacking height of up to 1-over-6, this height is seldom used in practice, with real-world stacking heights usually settling at around three to four containers high. With the four-high stacking capacity of the latest generation of Kalmar AutoStrad™, the difference in stack height is no longer that dramatic.
However, maximum capacity does not automatically translate into optimum efficiency or throughput. At many terminals, it is not possible to obtain information in advance on when a specific container will be needed at the landside, so the container needs to be retrieved whenever the road truck arrives for pickup. Often, the capacity gained with higher stacking results in a dramatic drop in productivity as time is lost on unproductive rehandling moves. At straddle carrier terminals, there is a relatively low percentage of non-productive container moves, as the containers are more easily accessed in the straddle carrier stacks.
Any shape or size
Compared to traditional terminal concepts, automated straddle carriers enable more efficient use of the terminal site, as they don't require the buffer or maintenance areas of large gantry cranes. Automated straddle carriers are also not limited to the fixed rectangular container blocks of ASCs and RTGs, so they are able to operate efficiently on sites of any shape.
This means that even though the theoretical maximum stacking density within the container block will be higher for an ASC, an AutoStrad™ concept may provide a roughly equivalent stacking density over the entire land area of the terminal. Automated straddle carriers also enable more streamlined handling of empty containers, with the empties stored in a separate manually operated area, and the transfers handled through a designated high-volume container exchange grid between the empty container stacks and the automated yard. Using this process, empty containers can be transferred very efficiently, and they don’t take up space for long in the automated yard.
Finally, automated straddle carriers are vastly superior in making use of terminal land area when compared to traditional manually operated straddles. As automated straddle carriers can drive safely at speed through the container stack, they don't require separate driving lanes between container blocks, which means that this space also can be utilised for container storage.
When considering the choice of automation solution and terminal concept for current and future megaterminals, it is important to remember that the question is not an either/or choice. Layouts combining multiple horizontal transportation or crane technologies are possible, and additional stacking capacity can easily be added to an AutoStrad™ terminal with an ASC block within the fully automated yard. In this scenario, the external container handling interfaces for quay and RMG cranes as well as for truck lanes remain unchanged, while enabling optimal usage of the terminal land area.
Related articles
Further reading
Subscribe and receive updates in your email
Subscribe